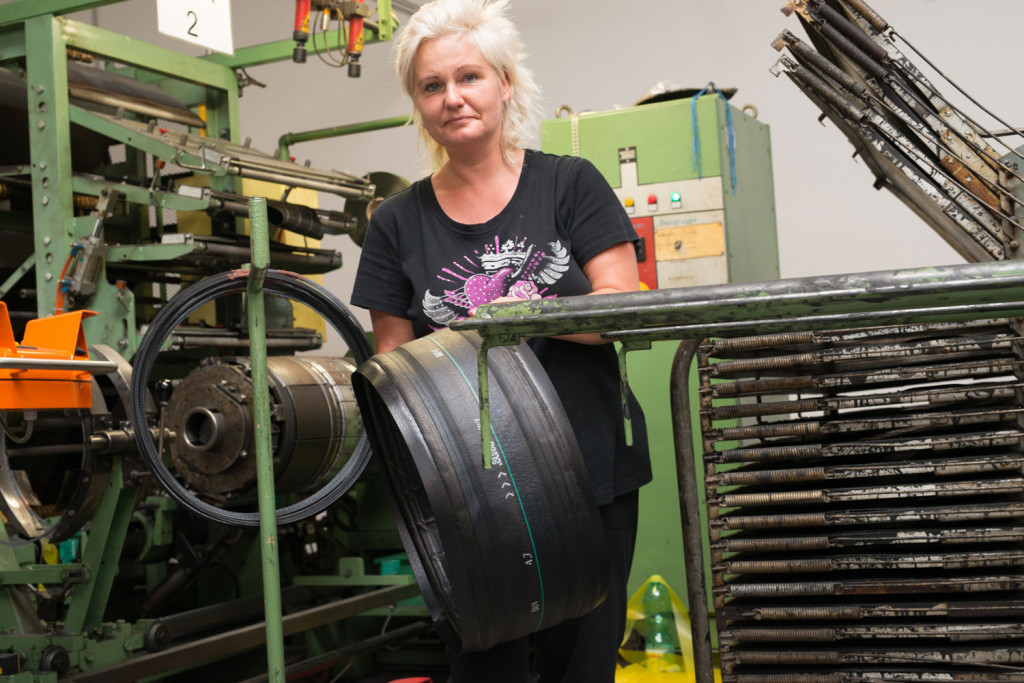
Pneus éprouvés de Saxe: reportage: 150 pneus DXP faits à la main par jour
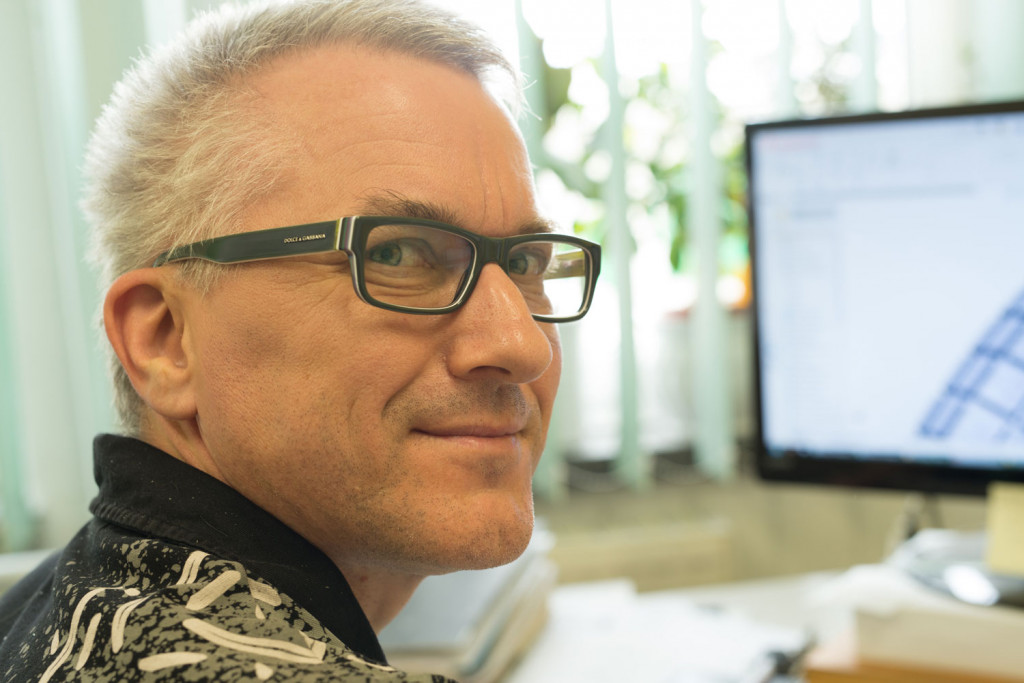
"KYBURZ avait des exigences bien précises. C'était particulièrement délicat de combiner la large zone de contact avec la jante étroite."
René Kaiser de la production de pneus Heidenau
Un travail attentif est exigé
La gomme est un produit naturel fait de caoutchouc. Pour chaque lot de matière première livré, un échantillon est testé dans notre laboratoire d'essai interne pour des facteurs tels que la résistance à la traction ou la dureté et les lots sont ainsi étiquetés avec précision. Un travail attentif est nécessaire, car le caoutchouc n'est plus qu'une masse noire et les différents mélanges ne se distinguent plus à l'œil nu.
Les tissus en nylon, polyester ou autres matériaux sont recouverts à l'avant et à l'arrière et collés avec du caoutchouc dans la calandre, une machine qui remplit tout le hall. "La sous-construction invisible constitue un pneu, le profil visible n'est que la couche supérieure ", explique Thomas Schoenherr. Pour le protecteur, c'est-à-dire la peau extérieure du pneu visible à l'extrémité, le caoutchouc passe à travers une extrudeuse qui presse le matériau à la forme souhaitée avec une pression allant jusqu'à 90 bars et des températures d'environ 100 degrés Celsius.
Jusqu'à cinq fils constituent le noyau du talon du pneu sur la jante. A Heidenau, les mécaniciens de l'entreprise fabriquent même l'outil spécial qui réunit les fils et les recouvre d'une couche de caoutchouc.
150 pneus DXP par jour – faits à la main
Dans le département de la confection, les employés assemblent ainsi à la main les composants préparés du pneu pour former la carcasse. Ramona Greiner travaille à l'usine de pneus depuis plus de 20 ans. "En fait, je connais l'ensemble du processus de production de pneumatiques ", explique la femme, qui a de nombreuses années d'expérience et qui peut être placée à tous les postes du montage.
"Beaucoup de nouvelles dimensions ont été ajoutées ces dernières années". Aussi le pneu pour le KYBURZ DXP. "J'aime faire du DXP ", dit-elle - 150 pneus sont produits dans ses mains chaque jour. D'abord, elle enroule l'âme autour du tambour. Deux couches de tissu à des angles différents composent la structure. Ramona Greiner arrache habilement les bandes de tissu à la main pour que les joints s'ajustent exactement. Si les couches se chevauchent, il y aurait un déséquilibre qui perturberait le comportement de conduite comme conséquence.
Les couches sont compressées. Il ne doit pas y avoir de plis ou de poches d'air. A l'aide d'un simple outil à roulettes, elle vérifie la qualité plusieurs fois au cours de la production. Après les deux fils et le tissu latéral pour le renforcement dans la zone de la jante, le protecteur est appliqué comme dernière couche. Ramona Greiner laisse tourner à nouveau le tambour, vérifie l'uniformité et voilà la carcasse d'un autre pneu DXP terminé.
Dernier point, mais non des moindres, la touche finale
Dans toutes les halles de production de l'usine de pneus, l'odeur bien connue du caoutchouc frais se fait sentir. L'odeur est particulièrement intense autour des presses chauffantes. Les moules négatifs métalliques avec la bande de roulement du pneu sont chauffés à la vapeur à environ 160 degrés Celsius. Le boudin, un bourrelet de caoutchouc remplie de vapeur, presse l'ébauche dans le moule de l'intérieur.
Pour que l'air puisse s'échapper, il y a des trous étroits dans le moule, qui sont alors visibles sous forme de poils fins à l'extérieur du pneu neuf. Le caoutchouc est vulcanisé, ou cuit comme le disent les employés. Pour chaque type de pneu, des spécifications précises concernant la pression, la température et la durée du processus doivent être respectées. Les réchauffeurs puissants enlèvent les pneus des presses à vapeur. Cependant, ils ne sont pas encore prêts pour le stockage.
Tom Weicheltstreich garde un œil attentif et une main sensible sur chaque pneu de la production. Toujours en train de rouler à la vapeur, les pneus sont soumis à un contrôle de qualité. La communication avec les collègues est très importante, dit-il, car seule une rétroaction immédiate peut prévenir les éventuels défauts.
Réorientation complète après la chute du mur de Berlin
La qualité doit être bonne ! Reifenwerk Heidenau fournit des pneus pour les véhicules électriques de KYBURZ Switzerland depuis environ 2000.
Aujourd'hui, plus de 200 employés produisent plus de 550 modèles de pneus pour des deux et trois roues, des voitures classiques, des karts et applications spéciales. Ce qui a commencé en 1946 avec la production de semelles de chaussures s'est transformé en une grande entreprise qui, dans les années 1980, produisait 10.000 pneus par jour avec plus de 800 employés. En tant que membre du groupe Pneumant, Heidenau a fourni à une grande partie du bloc de l'Est en pneus deux roues à l'époque de la RDA.
Les marchandises de haute qualité pourraient même être exportées vers l'Ouest. Des temps difficiles sont apparus après le changement politique : Les produits de l'Est n'étaient plus en demande. En 1994, l'entreprise n'employait plus que 104 personnes et la reprise de l'usine par les dirigeants et la réorientation constante vers les pneus pour les nouveaux scooters à moteur dans les années 1990 ont conduit à la réussite. "Nous faisons beaucoup de travail manuel dans la production ", explique Thomas Schoenherr, directeur des exportations. "L'automatisation se fait au détriment de la diversité. Cette diversité doit être préservée, car KYBURZ continue de compter sur la collaboration de Reifenwerk Heidenau pour l'avenir.
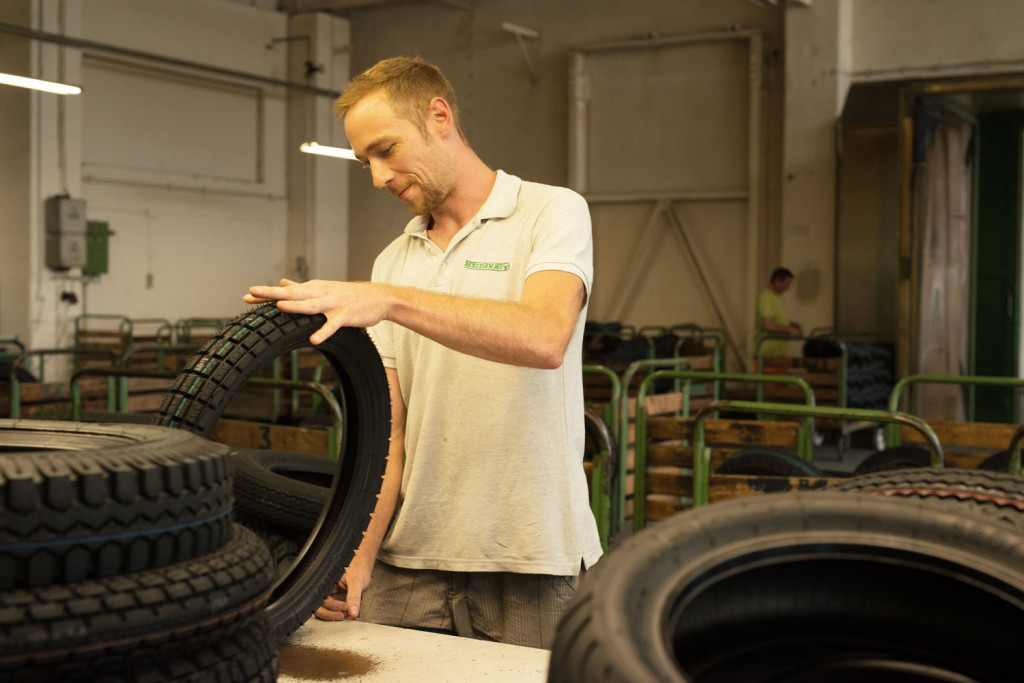