Batterie en feu
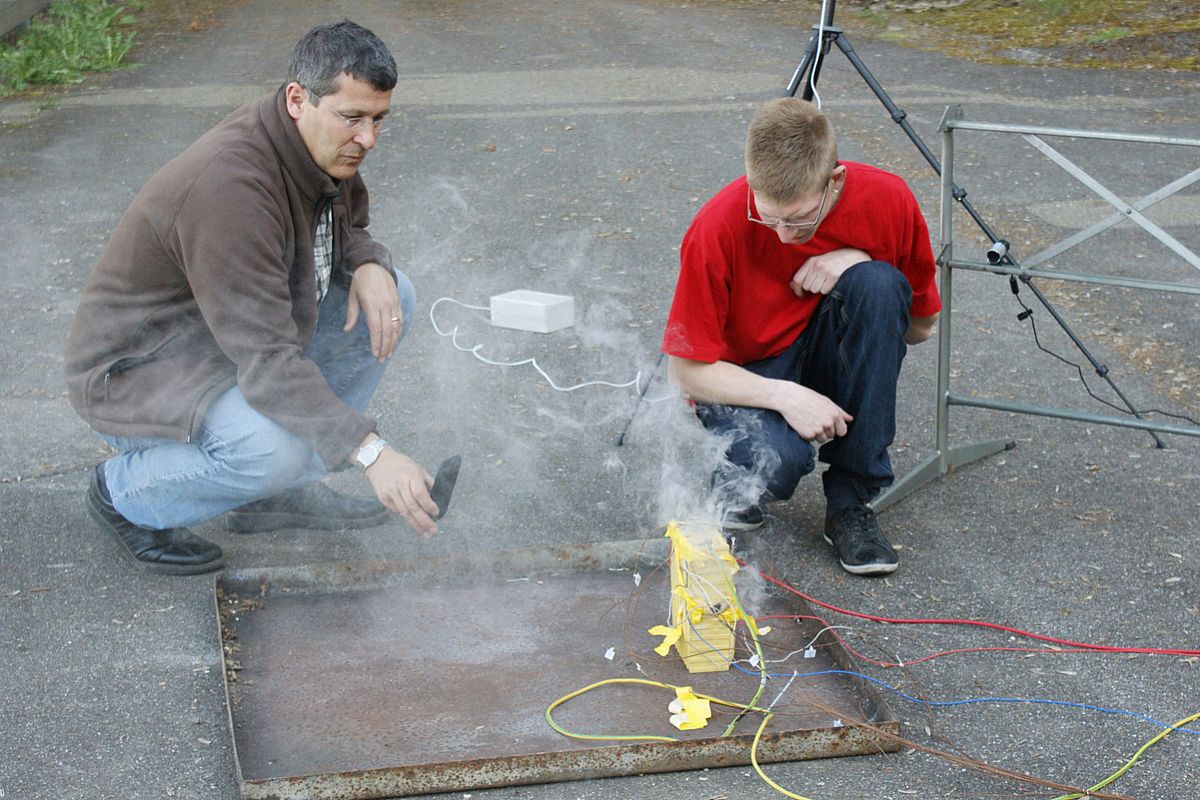
J’ai reçu un appel : un de nos véhicules DXP avait pris feu. Il ne s'était pas passé grand-chose. L'incendie a pu être détecté et rapidement éteint. Nous avons immédiatement envoyé un mécanicien pour récupérer le véhicule incendié. Lorsqu'il est arrivé chez nous, je me suis précipité vers le véhicule pour l'examiner. Après un premier coup d'œil, j'ai été frappé : il semblait qu'une des cellules avait pris feu. Ce n'était pas possible, n'est-ce pas ? Nous avions pourtant choisi des batteries LiFePO4 qui n'étaient pas inflammables. Que s'était-il donc passé ? J'ai tout de suite compris qu'il s'agissait d'une réaction en chaîne et que nous avions besoin d'aide, car nous ne pouvions pas résoudre le problème nous-mêmes. J'ai immédiatement téléphoné à l'EMPA. Un certain Monsieur Held m'a répondu. Il était exactement la personne qu’il nous fallait : un héros. Je lui ai expliqué la situation et le fait que nous avions besoin de soutien. Il m'a dit qu'il voulait de toute façon se familiariser avec ce domaine et qu'il prendrait le temps de nous aider à résoudre le problème. Au téléphone, nous avons convenu que la première chose à faire était de comprendre le processus. Nous devions pouvoir comprendre comment le véhicule avait pris feu. Pour cela, nous avons construit trois véhicules de test. Entre-temps, Marcel Held a réactivé un ancien terrain d'essai de l'EMPA, où des tests de munitions avaient été effectués dans les années 60. Le terrain se trouvait à l'extérieur de Dübendorf. Il n'avait plus été utilisé depuis de nombreuses années et était très délabré, il était situé au milieu de la forêt. C'était un endroit vraiment idyllique. Il a également organisé tout l'équipement de mesure afin d'immortaliser les événements. Quelques jours plus tard, nous nous sommes retrouvés sur le site. Nous avions apporté suffisamment de batteries et deux véhicules. Nous avons immédiatement commencé les tests. Nous avons d'abord enfoncé un clou dans une cellule. Comme on pouvait s'y attendre, elle a dégazé. Ensuite, nous avons surchargé une cellule. Nous avons pu la surcharger à un facteur six. Là encore, elle n'a pas brûlé. Elle a fondu comme un fromage et son intérieur a été mis à nu. Ensuite, un véhicule de test, dans la configuration actuelle a été testé. Pour documenter le tout, nous avions installé des caméras à l'intérieur du véhicule. Pour plaisanter, le collaborateur qui s'est procuré les caméras s'est demandé si les droits de garantie étaient également disponibles en cas d'incendie ? Le vendeur avait répondu par l'affirmative.
Nous avons planté un clou dans l'une des cellules et voilà qu'au bout de six minutes environ, le véhicule a commencé à prendre feu. Nous pouvions maintenant reproduire l'incendie et apprendre ainsi comment se déroulait la mise à feu. Après deux autres essais, nous avons constaté que la cellule se dégazait normalement. Une partie de l'électrolyte chaud avait été projetée sur le BMS de la batterie. Comme l'électrolyte était chaud, il était très agressif et a fait fondre le vernis de protection. Cela a eu pour effet de rendre le BMS conducteur. Le courant a commencé à s'échapper des cellules encore saines. Nous avons mis un couvercle sur les batteries. Mais celui-ci empêchait le gaz qui s'échappait de se volatiliser. En raison de la chaleur, de petites quantités d'hydrogène se sont également formées et ont été allègrement recueillies dans le couvercle de la batterie. Le courant électrique qui s'écoulait par le BMS continuait à chauffer le gaz : De 250 degrés à plus de 750 degrés. C'est à ce moment-là que l'hydrogène s'enflamme et se consume. Cette déflagration - en fait très inoffensive - a suffi, avec la température déjà très élevée, à enflammer le faisceau de câbles. Celui-ci brulait lentement, comme une mèche, et a ensuite mis le feu à une pièce ABS, qui a finalement enflammé tout le véhicule. Il nous a fallu deux jours pour comprendre exactement ce qui s'était passé. Il fallait maintenant y remédier : Nous avons choisi un autre vernis de protection pour les impressions, modifié les couvercles de batterie afin de bien évacuer le gaz en cas de dégazage et modifié certains matériaux pour les rendre difficilement inflammables. Exactement une semaine plus tard, nous avions trouvé les mesures correctives efficaces et les avions testées avec succès.
Il restait encore une énigme à résoudre : Chaque soir après la série d'essais, nous mangions ensemble un kebab à Dübendorf. Je me sentais mal à chaque fois. Au début, je pensais que c'était à cause du kebab. Mais apparemment, les autres membres de l'équipe étaient dans le même état. Nous avons demandé à un chimiste de l'EMPA et sa couleur de peau a changé : il est devenu blanc comme un linge. Est-ce que nous avions perdu la tête ? Nous ne pouvions réaliser une telle expérience qu'avec des dispositifs de protection. Le gaz produit contient probablement de l'acide fluorhydrique, qui est très toxique. J'ai demandé s'il pouvait y avoir des dommages à long terme. Le chimiste a répondu par la négative. Soit nous étions morts sur le coup, soit nous survivions. On ne connaissait pas les conséquences à long terme.
Nous avons pris à cœur les instructions du chimiste et lors des expériences suivantes, nous avons d'abord regardé d'où venait le vent. Par sécurité, nous avons aussi installé quelques ventilateurs et nous nous sommes retrouvés dans la zone où les gaz ne s'accumulaient pas. Le soir, nous avons pu savourer notre kebab.
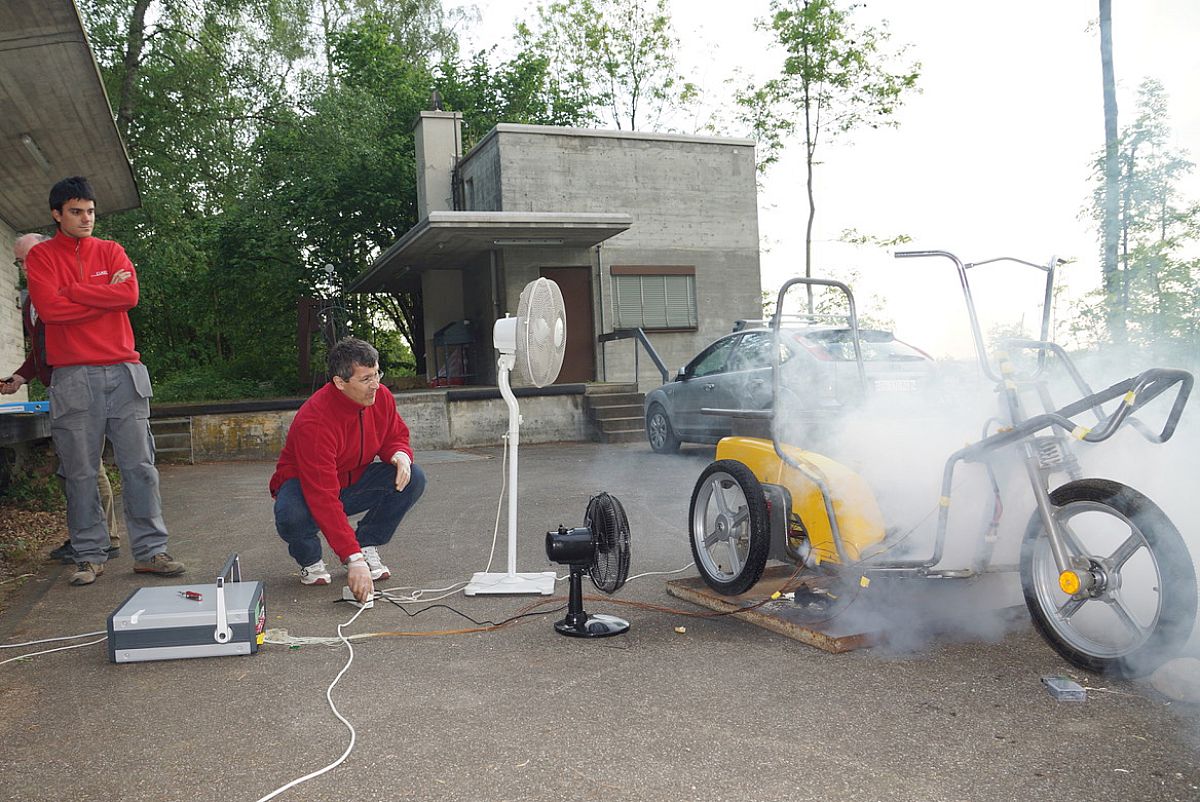
Nous savions alors ce que nous devions faire. Il ne nous restait plus qu'à équiper les 1700 véhicules déjà livrés. J'ai vivement conseillé au client de placer les extincteurs à côté des véhicules et de ne les charger que lorsque quelqu'un se trouvait à proximité. Les clients ont réagi avec inquiétude. Un tel changement n'était pas réalisable à la hâte et il fallait d'abord trouver un budget pour les extincteurs.
Entre-temps, nous avons effectué une tournée de mise à niveau à grande échelle. Nous avons recruté du personnel et formé jusqu'à 8 groupes de 2 à 4 personnes. Nous avons écrit à nos fournisseurs et certains ont mis leur personnel à disposition. Nous avons également renforcé le personnel administratif. Enfin, il fallait écrire à tous les clients et les informer de l'action à venir. J'ai appelé d'anciennes connaissances pour leur demander si elles n'étaient pas prêtes à travailler pour moi. Deux personnes qui ont spontanément accepté à l'époque font encore partie de notre équipe aujourd'hui, plus de dix ans plus tard. Chez nous, devant l'atelier, nous nous sommes exercés à la mise à niveau sur nos propres véhicules. Les temps ont été chronométrés, le travail a été peaufiné et tout a été documenté.
J'ai acheté deux véhicules de transport supplémentaires pour équiper les huit équipes et quelques jours plus tard, les équipes se sont mises Après exactement huit semaines, les 1700 véhicules étaient équipés. Nous étions fiers de notre performance. Peu après l'achèvement, j'ai reçu la confirmation de notre plus gros client qu'ils avaient entre-temps le budget et pouvaient se procurer les extincteurs. Je lui ai simplement répondu que ce n’était plus nécessaire.
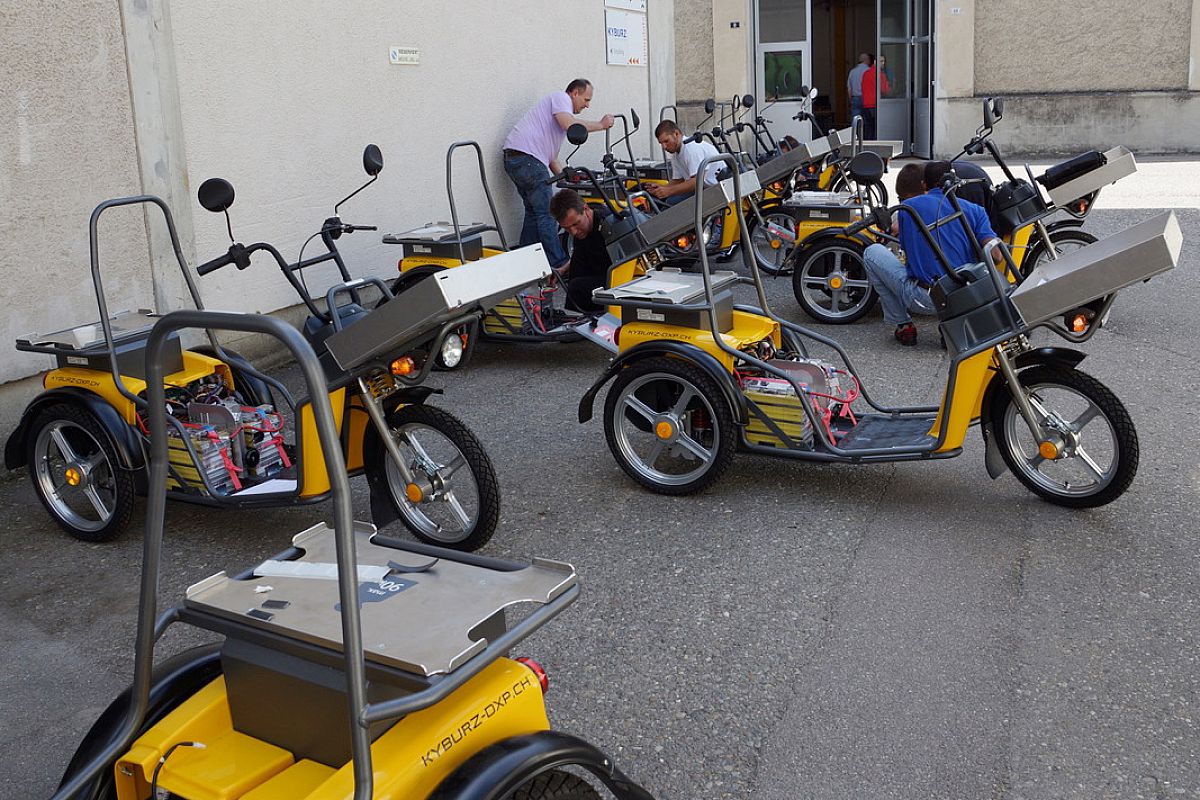
Ce que j’ai appris
- Si l'on travaille bien en équipe, le succès est au rendez-vous.
- Faire la fête est également important. Cela permet de faire le plein d'énergie.
- Je dois garder à l'esprit mon équilibre entre vie professionnelle et vie privée.
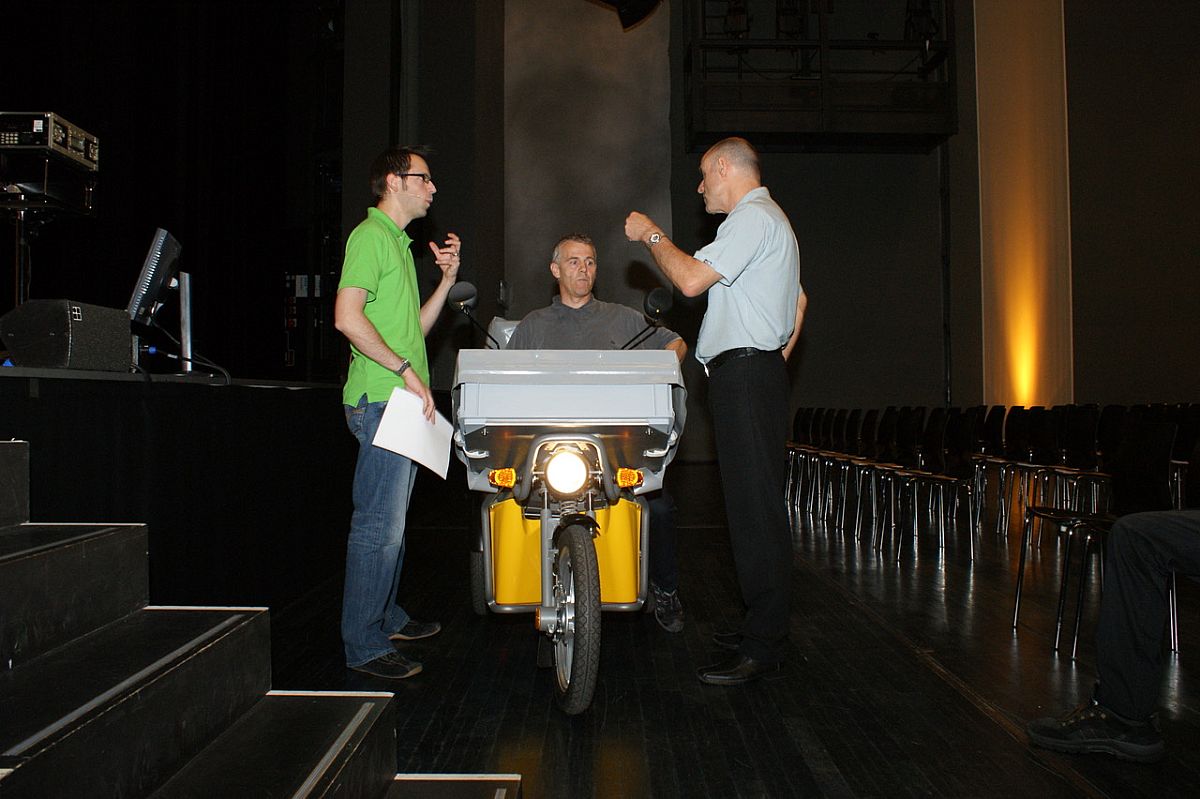
J'en ai tiré la leçon :
- De temps en temps, un vrai héros peut aider.
- En cas d'incendie, il faut garder la tête froide.
- Le test avec des clous ne doit pas être effectué uniquement sur des cellules de batterie individuelles, mais sur l'ensemble du véhicule, afin d'inclure également l'environnement dans le test.