Recyclage des batteries
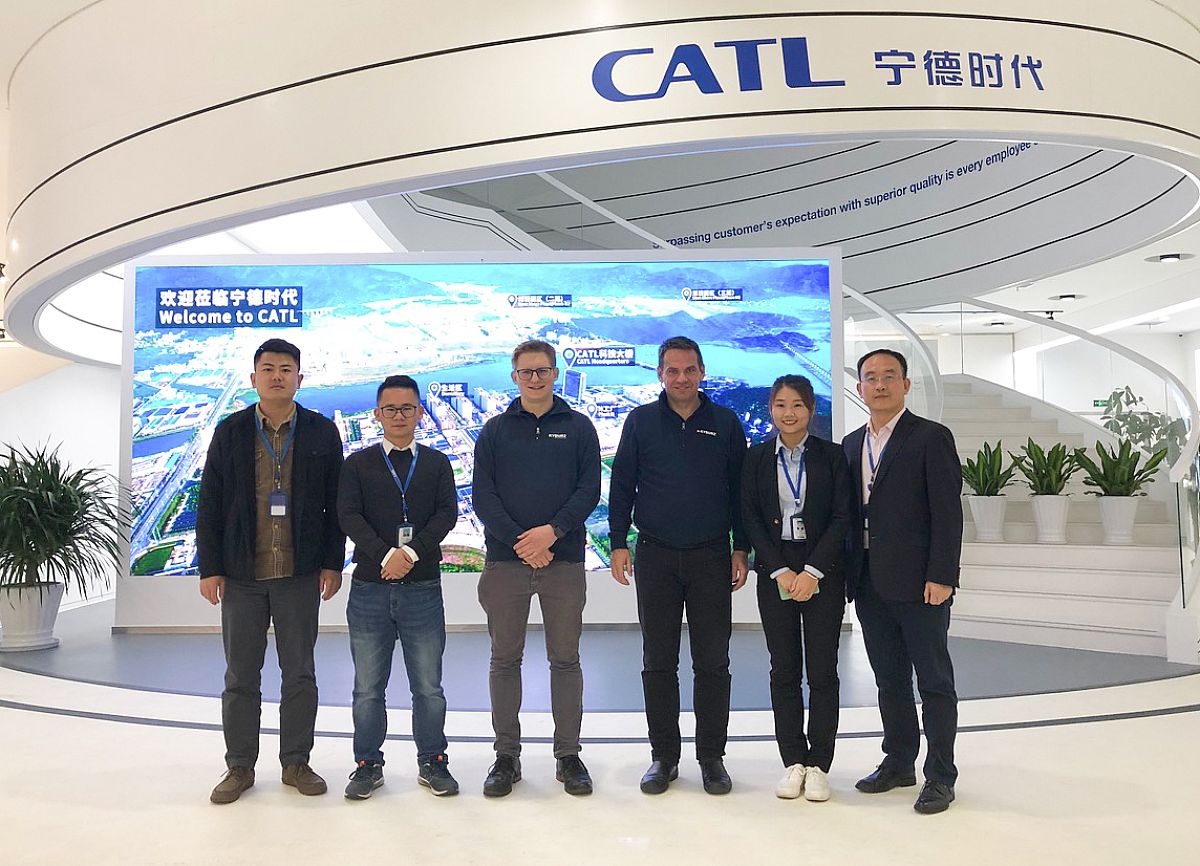
Qu'en est-il de la taxe anticipée de recyclage prélevée sur les batteries ? Importions-nous nos batteries sur le marché gris ? La rumeur a circulé que nous n'avions pas payé de taxe anticipée de recyclage. Je me suis renseigné auprès d'Inobat, qui est responsable de la perception de ces taxes. La situation s'est présentée comme suit : Nous étions tout simplement l'une des premières entreprises à utiliser des batteries au lithium pour nos véhicules et la manière dont Inobat entendait traiter cette question n'était tout simplement pas encore réglée. Peu de temps après, il a été décidé que nous devions également payer ces taxes et tout a été réglé.
J'ai donc voulu savoir où les batteries étaient recyclées et comment les matériaux utilisés dans la production de nos batteries étaient récupérés. Avec Claudia Fesch, notre responsable des contrats, j'ai visité à Thoune la seule usine de recyclage de batteries en Suisse. Nous avons vu un immense haut fourneau très impressionnant, exploité par la société BATREC. Toutes les batteries y étaient incinérées et un peu de matière pouvait effectivement être récupérée. Mais on y produisait surtout des cendres qui devaient être stockées quelque part. Nous étions tous les deux horrifiés par le gaspillage pur et simple.
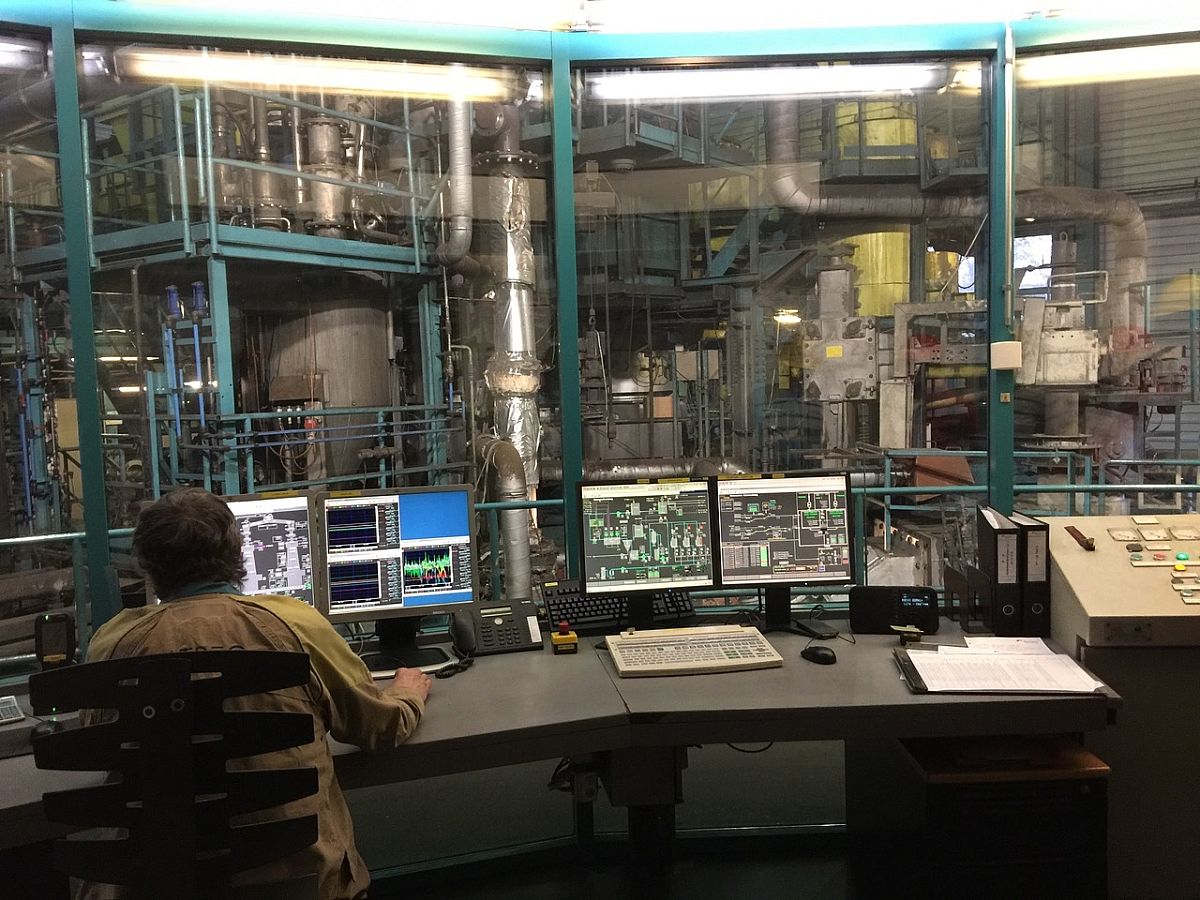
Peu après j’étais avec Rolf Widmer et Marcel Gauch de l'EMPA à Nuremberg pour un séminaire sur les derniers développements en matière de batteries, avec pour thème principal le vieillissement des batteries au lithium. La veille de la manifestation, nous étions ensemble au restaurant.
Pendant le dîner, l'idée suivante est née : La meilleure façon de recycler les batteries était de les démonter exactement comme elles ont été assemblées. Cela semblait simple, mais l'était-ce vraiment ? Nous voulions le savoir ! Un peu plus tard, Marcel Gauch s'est manifesté : il avait été contacté par un étudiant en technique environnementale. Cet étudiant cherchait un travail sur les batteries lithium-ion. Il avait rédigé un travail de semestre sur la seconde vie des batteries et avait déjà ouvert et démonté des batteries dans sa cave.
Cela pouvait-il être le début d'un essai de recyclage de nos batteries ? Les modalités ont été réglées et peu après, Olivier Groux s'est présenté. Il présentait les conditions idéales pour cette tâche : avant ses études, il avait appris le métier de laborantin en chimie. Il était familier avec toutes les substances chimiques qui se trouvaient probablement dans une cellule de batterie. Il avait également des notions d'électrotechnique et de mécanique. A la fin de son travail de diplôme, Olivier nous avait prouvé que la théorie fonctionnait. En outre, il avait trouvé par hasard un procédé permettant de dissoudre le matériau actif, le graphite pour le cuivre (anode) et le phosphate de fer pour l'aluminium (cathode).
J'étais ravi ! Olivier a terminé ses études et a été récompensé par la meilleure note. Il a alors commencé un nouveau poste de conseiller en énergie pour la ville de Berne.
Après cela, ses adresses e-mail n'étaient malheureusement plus valables et il m'a fallu un peu de temps pour retrouver son adresse : je lui ai alors proposé un emploi s'il développait pour moi une installation de recyclage des batteries que nous utilisons. Olivier n'a pas eu besoin de beaucoup de temps de réflexion. Un budget a été négocié pour développer et construire l'installation et Olivier s'est mis au travail. En collaboration avec l'EMPA, il a élaboré le processus. Il s'est rendu en Chine et a visité de nombreux fabricants de batteries afin d'étudier plus en détail le processus de production. Un jour, j’ai reçu un appel de Chine. Olivier était au téléphone. Il avait également rendu visite à notre fabricant de batteries, chez qui nous nous fournissions en cellules depuis de variées années. Il y avait quelque chose de bizarre : il avait vu l'installation de production, mais elle avait été transformée pour une autre chimie. Cela m'a mis la puce à l'oreille. Les batteries sont un produit essentiel pour nos véhicules. Nous avons convenu qu'il devait prolonger son séjour d'un mois et que je me rendrais de plus en Chine avec Philipp Heim afin de discuter avec les fournisseurs de batteries. Comme le visa d'Olivier avait expiré, il s'est rendu à Tokyo pour y faire du télétravail et attendre son nouveau visa. Entre-temps, Philipp et moi sommes arrivés en Chine et nous avons visité ensemble cinq autres producteurs de batteries. Nous avons beaucoup appris, notamment sur la structure du marché des batteries en Chine. La construction de batteries est considérée comme un élément clé en Chine et est donc encouragée par l'État. Pour nous, cela signifiait que nous pouvions obtenir des batteries lithium-ion de haute qualité à un prix très avantageux. Pour les fabricants, cela signifiait que s'ils atteignaient leur objectif de production, ils recevaient davantage de subventions de l'État. C'était ainsi positif pour les deux parties. Chacun des fabricants venait de construire une nouvelle usine de production, et nous entendions souvent parler de centaines de millions d'euros investis dans une usine de production. À l'époque, personne ne s'intéressait au recyclage des matières premières. Le plus grand producteur de batteries que nous avons visité était l'entreprise CATL. Elle comptait plus de 30 000 employés, soit une ville entière. Nous avons visité quelques laboratoires et avons constaté que CATL était certainement la plus avancée dans son développement. Depuis, CATL est devenu notre nouveau fournisseur principal.
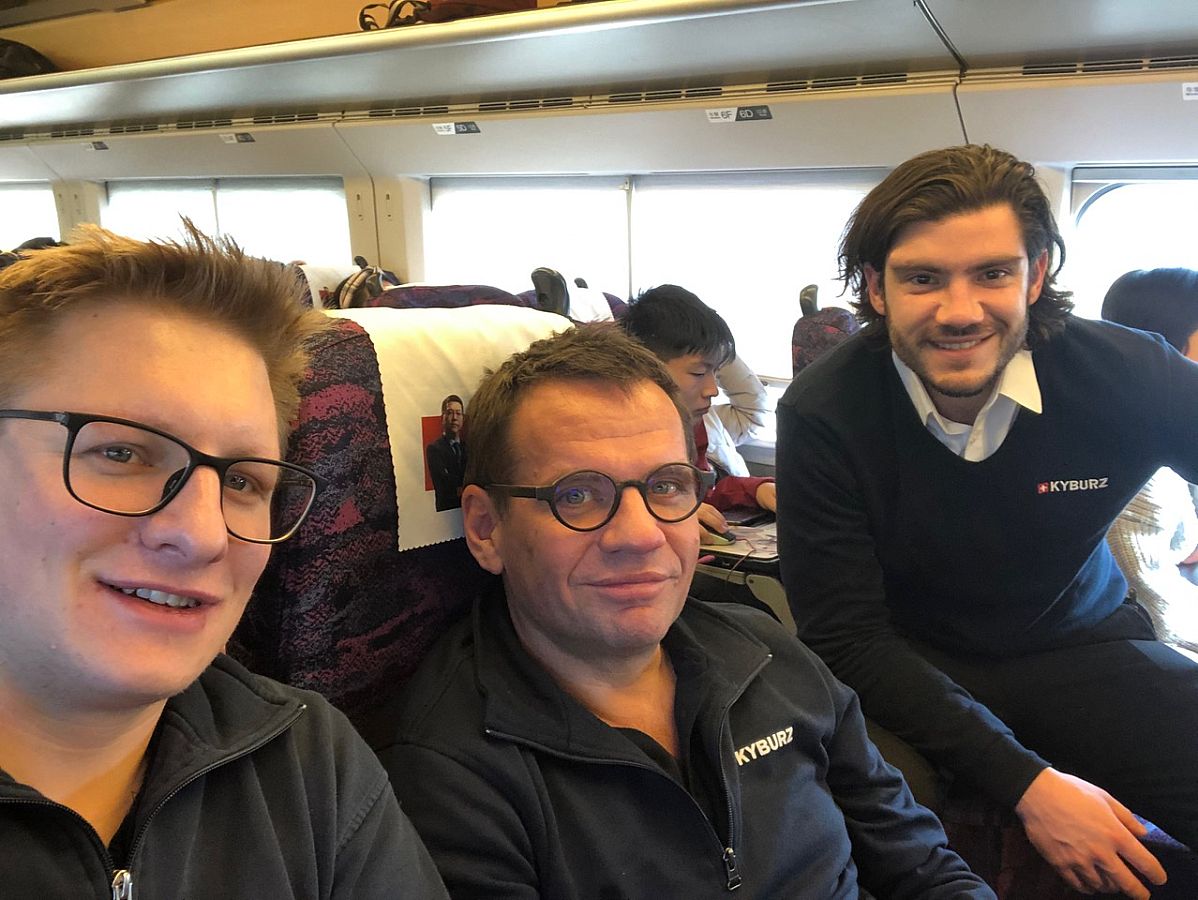
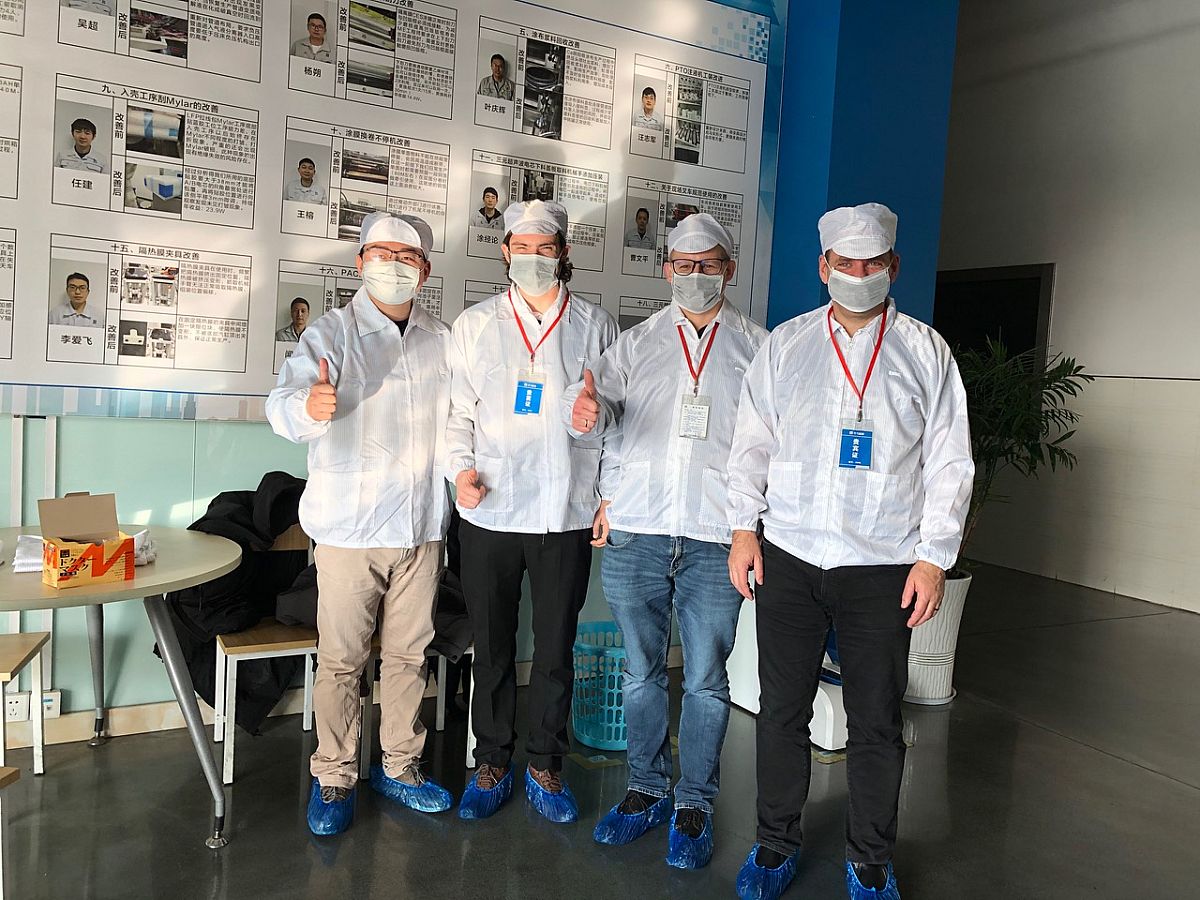
Nous sommes donc rentrés heureux à Freienstein. Non seulement nous avions trouvé un nouveau fournisseur de batteries exceptionnel, mais nous avions aussi beaucoup appris sur la production des batteries. Un savoir qu'Olivier a pu utiliser à merveille pour son processus de recyclage. Toutes ces connaissances ont été partagées avec l'EMPA et ensemble, ils ont créé un poster montrant et expliquant notre processus de recyclage. Un jour, Olivier m'a demandé si je ne voyais pas d'inconvénient à ce que l'EMPA et nous-mêmes présentions ensemble cette affiche dans le cadre d'un concours visant à mettre en évidence un processus inédit. Bien sûr, je n'avais rien contre. Je voulais que le savoir se répande. L'EMPA a participé au concours et a remporté le premier prix. Ce prix nous a fait plaisir - mais il avait aussi son revers. Nous avions confié un mandat de recherche à l'EMPA de Dübendorf, mais pas encore à l'EMPA de Saint-Gall. La direction est intervenue et nous avons dû passer une commande à Saint-Gall également. Le premier prix que nous avons obtenu nous a donc coûté une somme considérable.
A l'automne 2020, notre symposium sur l'économie circulaire a eu lieu à Freienstein. A cette occasion, j'ai voulu présenter notre installation de recyclage lors d'une conférence de presse. Nous avons fait construire la machine proprement dite par l'entreprise Welthaupt en Appenzell. Tout serait-il terminé à temps ? Tous les participants ont répondu par l'affirmative, mais plus le délai approchait, plus le travail était frénétique. L'entreprise Welthaupt avait besoin de soutien et l'un de nos collaborateurs a travaillé pendant des mois avec eux, sans aucune bureaucratie, afin de monter la machine dans les temps. Comme c'est souvent le cas dans ce genre de projet, le temps était compté. J'ai insisté pour que la machine soit déjà montée et disponible pour une séance photo avant la conférence de presse proprement dite. Le directeur de Welthaupt disait que c’était possible, mais qu'il fallait démonter la machine pour le transport vers Freienstein et ensuite à nouveau la démonter pour la ramener dans son atelier en Appenzell afin de la terminer. Non, cela n’était que du travail supplémentaire et je ne voulais pas charger les personnes impliquées dans le projet d’autres difficultés dans la phase finale décisive. Les collaborateurs de l'entreprise Welthaupt pouvaient continuer à construire et notre photographe devait faire preuve d'une grande flexibilité.
Peu avant la conférence de presse, la machine a été montée et rosée. Samuel, le directeur de la société Welthaupt, était l'opérateur. C'est lui qui connaissait le mieux la machine. Le photographe a obtenu ses photos et les documents ont pu être réalisés juste à temps. J'ai vu la machine fonctionner pour la première fois le jour de la conférence de presse, tout comme Marcel et Rolf de l'EMPA, et nous étions tous très enthousiastes. Voir les cellules de la batterie disparaître dans la machine et disposer à la fin du processus de toute la matière première sous forme pure a été la grande récompense de toutes les gouttes de sueur versées par l'équipe d'Olivier Groux. Le meilleur dans tout cela : La machine fonctionne aujourd'hui exclusivement à l'énergie solaire et aucun produit chimique n'est utilisé pour le démontage. Elle n’a besoin que d’eau.
Nous n’avons délibérément pas rédigé de brevet de procédé. Nous mettons ce savoir à la disposition du monde entier. De nos jours, il est vital pour l'homme de recycler au mieux les batteries usagées.
J'en ai tiré la leçon :
- Chez nous, les projets complexes ne sont toujours terminés que quelques minutes avant la présentation.
- La Suisse possède de nombreuses matières premières - transformées en batteries. Il suffit de les récupérer.
- De temps en temps, je suis surpris par le succès d'un projet.